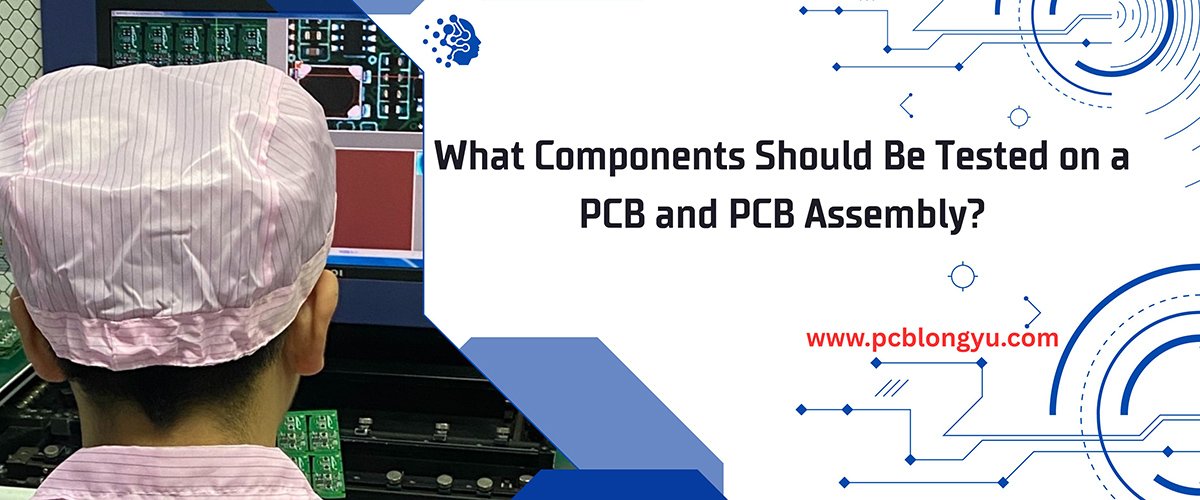
PCB and PCBA: An Overview
A Printed Circuit Board (PCB) is the foundational platform used to mechanically support and electrically connect electronic components using conductive pathways, tracks, or signal traces etched from copper sheets laminated onto a non-conductive substrate. PCBs can range from simple single-layer boards to complex multi-layer configurations, depending on the application. When all the electronic components, such as resistors, capacitors, ICs, and connectors, are soldered onto the PCB, it becomes a Printed Circuit Board Assembly (PCBA). The process of turning a bare PCB into a functional PCBA involves component placement, soldering (either through-hole or surface-mount technology), inspection, and testing. While the PCB serves as the skeleton of an electronic device, the PCBA represents the fully assembled, functional electronic module ready for integration into electronic systems.
In electronics manufacturing industry, ensuring the performance and reliability of printed circuit boards (PCBs) and their assemblies is crucial. Testing plays a vital role in detecting defects, verifying design functionality, and maintaining quality standards before products reach the market. To achieve this, various components and aspects of the PCB and its assembly must be thoroughly tested throughout the production cycle.
What Components Should Be Tested on a PCB and PCB Assembly
PCB and PCBA component testing is a critical process in electronics manufacturing that ensures the reliability, functionality, and quality of circuit boards and their assemblies. During testing, both passive components (such as resistors, capacitors, and inductors) and active components (like diodes, transistors, ICs, and microcontrollers) are examined for correct values, proper orientation, and electrical performance. Additionally, solder joints, connectors, and PCB traces are inspected for continuity, shorts, or physical defects using techniques like automated optical inspection (AOI), in-circuit testing (ICT), and X-ray analysis. Thorough component testing helps identify manufacturing defects early, minimizes product failure in the field, and ensures the final product meets design and safety standards.
Passive Components
Resistors, capacitors, and inductors are among the most common passive components used in PCBs. These elements must be tested to confirm:
· Correct value: Verifying resistance, capacitance, and inductance ratings.
· Tolerance: Ensuring values fall within acceptable variance ranges.
· Positioning and polarity (for polarized capacitors): Especially important for electrolytic and tantalum capacitors.
Testing methods may include automated optical inspection (AOI), in-circuit testing (ICT), and LCR (Inductance, Capacitance, Resistance) meters.
Active Components
Semiconductors, such as diodes, transistors, and integrated circuits (ICs), require meticulous testing due to their complexity and functionality.
· Functional Testing: Ensures that each component performs its intended operation under load conditions.
· Pin Continuity & Short Circuit Detection: Confirms proper soldering and absence of unintended bridges between pins.
· Thermal Behavior: Detects overheating or instability during power application.
Specialized test benches or boundary scan techniques are often used for these components.
Connectors and Sockets
Connectors are critical for interfacing with other hardware components. Faulty connectors can lead to intermittent or complete signal failure.
· Mechanical Integrity: Checks for loose, misaligned, or improperly soldered connectors.
· Continuity Testing: Ensures proper electrical connections.
· Insertion/Extraction Force Testing: Verifies durability and usability.
Power Supply Circuits
Power integrity is fundamental for any electronic device. Power circuits are tested to confirm:
· Voltage Levels: All supply rails are within specified tolerance.
· Current Draw: Ensures no abnormal current that may indicate a short.
· Ripple and Noise: Measures stability of output, especially for sensitive analog circuits.
DC power analyzers or oscilloscopes are commonly used to assess power performance.
Microcontrollers and Programmable Devices
Microcontrollers, FPGAs, and other programmable ICs should be tested not only for correct installation but also for:
· Programming Verification: Confirms correct firmware or logic has been loaded.
· Boot and Communication Tests: Ensures the device can initialize and communicate as intended.
JTAG, ISP (In-System Programming), and functional test jigs are used for such verification.
Solder Joints
One of the most common failure points in PCB assemblies is solder joints.
· Visual Inspection (Manual/AOI): Identifies cold solder joints, solder bridges, or insufficient solder.
· X-ray Inspection: Useful for hidden joints, such as those found in BGAs (Ball Grid Arrays).
· Micro-section Analysis: Used in failure analysis to inspect cross-sections of solder joints.
PCB Traces and Vias
The copper traces and vias must be tested for integrity and performance.
· Continuity and Isolation Testing: Detects open or short circuits.
· Impedance Testing: Critical for high-speed or RF circuits.
· Layer Alignment: Ensures multi-layer boards are fabricated correctly.
Environmental and Stress Testing
Beyond electrical testing, PCBs may be subjected to:
· Thermal Cycling: Simulates operating temperature variations.
· Vibration and Shock Testing: Ensures mechanical durability.
· Humidity and Corrosion Tests: Evaluates performance in harsh environments.
PCB and PCBA Component Testing Overview
Component/Area | What to Test | Testing Methods |
Passive Components | Value, tolerance, polarity (if applicable), placement | AOI, ICT, LCR meter |
Active Components | Functionality, pin continuity, thermal behavior | Functional Test, Boundary Scan, Test Benches |
Connectors & Sockets | Electrical continuity, mechanical integrity, insertion/extraction force | Continuity Test, Mechanical Inspection |
Power Supply Circuits | Voltage levels, current draw, ripple, noise | Oscilloscope, DC Power Analyzer |
Programmable Devices | Programming status, boot functionality, communication interfaces | JTAG, ISP, Functional Test Jigs |
Solder Joints | Cold joints, solder bridges, hidden faults (e.g., BGA), joint strength | AOI, X-ray, Micro-section Analysis |
PCB Traces & Vias | Continuity, shorts, impedance, layer alignment | Flying Probe, ICT, TDR (Time-Domain Reflectometry) |
Environmental Stress | Thermal, vibration, humidity resistance | Thermal Cycling, Shock/Vibration, Environmental Chamber |
Testing is an indispensable part of PCB and PCB assembly production. By systematically evaluating passive and active components, solder joints, power circuits, and overall board integrity, manufacturers can significantly reduce failures, improve product reliability, and enhance customer satisfaction. Integrating thorough and automated testing processes early in production not only saves time and cost but also ensures high-quality standards are consistently met.
Choose PCBLongyu — because we offer the best testing facilities in the industry. Our advanced inspection systems and rigorous quality control processes ensure that every PCB and PCBA meets the highest standards of performance and reliability. From automated optical inspection (AOI) and in-circuit testing (ICT) to X-ray analysis and functional testing, we leave no component unchecked. With PCBLongyu, you’re not just getting a product — you’re getting guaranteed precision, durability, and peace of mind. Trust us to power your innovation with excellence.