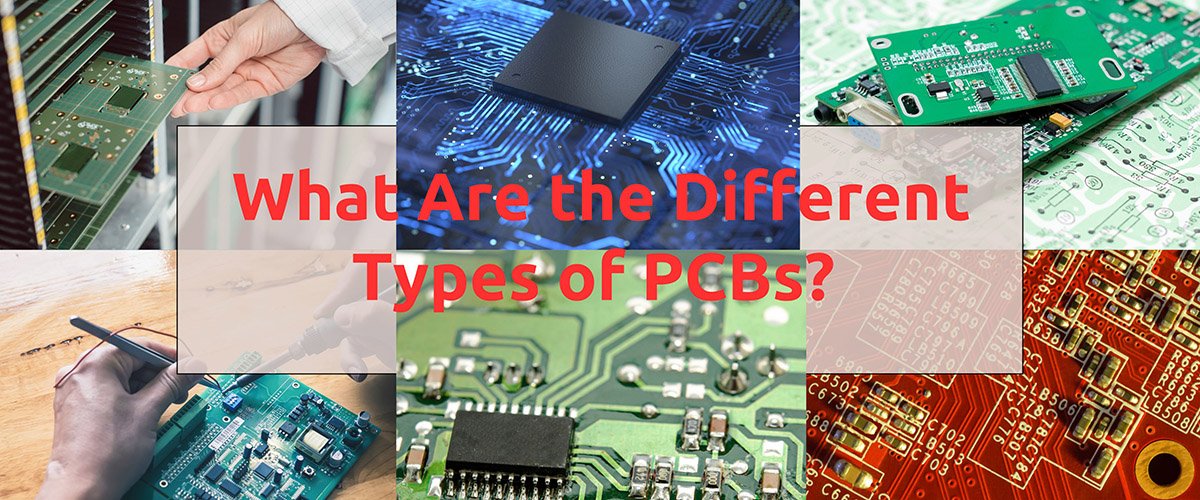
Printed Circuit Boards (PCBs) are essential components in modern electronics. They provide the foundation for connecting and supporting various electronic components through conductive pathways. Depending on the application, environment, and design requirements, PCBs come in different types. Understanding these types helps engineers and manufacturers choose the right one for their projects.
Below is a detailed look at the different types of PCBs, each with its own unique structure, material, and use cases.
Single-Sided PCBs
Single-sided PCBs are the simplest and most commonly used type of printed circuit board. They consist of a single layer of conductive material, typically copper, on one side of an insulating substrate such as FR4. The electronic components are mounted on one side of the board, while the copper traces on the opposite side form the circuit pathways. Due to their straightforward design, single-sided PCBs are inexpensive to manufacture and easy to produce in large volumes. However, they offer limited circuit complexity and are best suited for low-density, low-power applications. Common uses include basic household electronics, calculators, power supplies, and toys, where advanced functionality is not required.
Single-sided PCBs have only one layer of conductive material, typically copper, on one side of the board. Components are mounted on one side, and the circuit is etched on the other.
Advantages:
· Low cost
· Easy to design and manufacture
· Suitable for simple electronics
Applications:
· Calculators
· Power supplies
· Household electronics
Double-Sided PCBs
Double-sided PCBs, also known as double-layer PCBs, are circuit boards that feature conductive copper layers on both the top and bottom surfaces. Unlike single-sided boards, they allow for more complex circuit designs because components and traces can be placed on both sides, connected through vias (small holes drilled through the board). This design provides greater flexibility and higher circuit density, making them ideal for moderately complex electronic devices. Double-sided PCBs are widely used in applications such as LED lighting systems, industrial controls, power supplies, and automotive dashboards. Their balance of performance and cost makes them a popular choice in a variety of industries.
Double-sided PCBs have conductive layers on both sides of the board. Components can be mounted on either side, and vias (holes) allow connections between the layers.
Advantages:
· More circuit density than single-sided
· Better flexibility in design
· Suitable for moderately complex devices
Applications:
· Industrial controls
· LED systems
· HVAC systems
Multilayer PCBs
Multilayer PCBs are advanced circuit boards that consist of three or more conductive layers stacked together with insulating materials in between. These layers are laminated under high temperature and pressure to form a compact, unified structure. Unlike single or double-sided PCBs, multilayer boards offer higher circuit density and better design flexibility, allowing for more complex and powerful electronic systems in a smaller footprint. They also reduce electromagnetic interference and support high-speed signal transmission, making them ideal for sophisticated devices such as smartphones, medical equipment, servers, and aerospace electronics. Their ability to handle complex circuits while saving space has made them a standard choice in modern electronics.
Multilayer PCBs contain three or more conductive layers, separated by insulating material. These are laminated together to form a single board.
Advantages:
· High component density
· Reduced board size
· Ideal for complex and high-speed circuits
Applications:
· Smartphones and tablets
· Medical devices
· Servers and data storage
Rigid PCBs
Rigid PCBs, or Rigid Printed Circuit Boards, are the most commonly used type of PCB, characterized by their solid and inflexible structure. Made from durable materials such as fiberglass (FR4), rigid PCBs maintain their shape and cannot be bent or twisted, making them ideal for applications where structural stability is crucial. These boards offer a stable platform for mounting and interconnecting electronic components, ensuring reliable performance over time. Their robustness and long lifespan make them suitable for a wide range of electronic devices, including desktop computers, televisions, medical instruments, and automotive electronics. Due to their ease of manufacturing and cost-effectiveness, rigid PCBs continue to be a popular choice in the electronics industry.
Rigid PCBs are made from solid, inflexible materials (like FR4 fiberglass), meaning they cannot bend.
Advantages:
· Durable and strong
· Stable structure
· Long lifespan
Applications:
· Desktop computers
· Military devices
· Automotive controls
Flexible PCBs
Flexible PCBs, also known as flex circuits, are designed using bendable materials such as polyimide or polyester films, allowing them to twist, fold, and conform to various shapes. Unlike rigid boards, flexible PCBs can fit into compact or irregularly shaped spaces, making them ideal for modern miniaturized electronic devices. They are lightweight, reduce the need for connectors, and can withstand vibrations and movement, which enhances the overall durability and reliability of the product. Flexible PCBs are commonly used in applications like wearable devices, medical equipment, smartphones, cameras, and aerospace systems where space, weight, and flexibility are critical design factors.
Flexible PCBs are made of bendable materials like polyimide. They can be shaped, twisted, or folded.
Advantages:
· Lightweight and compact
· Can fit into tight or irregular spaces
· Absorb vibrations
Applications:
· Wearable electronics
· Cameras
· Flexible displays
Rigid-Flex PCBs
Rigid-Flex PCBs are a hybrid type of circuit board that combines the durability of rigid boards with the flexibility of flexible circuits. This design allows for both stiff and bendable sections within a single PCB, making it ideal for compact and complex electronic devices where space and weight are critical factors. Rigid-Flex PCBs eliminate the need for connectors and cables between board sections, enhancing reliability and reducing assembly time. These PCBs are commonly used in high-performance applications such as aerospace, medical devices, military systems, and modern consumer electronics, where mechanical stability and flexibility are essential.
Rigid-flex PCBs combine the features of rigid and flexible boards. A typical design has rigid sections connected by flexible layers.
Advantages:
· High reliability
· Compact design
· Reduced need for connectors
Applications:
· Aerospace and defense
· Medical implants
· Mobile phones
Aluminum-Backed PCBs (Metal Core PCBs)
Aluminum-Backed PCBs (Metal Core PCBs) are a type of printed circuit board designed with a metal base—usually aluminum—instead of the traditional fiberglass (FR4) substrate. This metal core acts as a heat sink, providing excellent thermal conductivity and helping to dissipate heat away from high-power components. Because of their superior heat management, aluminum PCBs are ideal for applications where thermal performance is critical, such as LED lighting, power supplies, and automotive systems. In addition to thermal benefits, they offer increased durability and mechanical stability, making them suitable for harsh environments. Their cost-effectiveness and performance advantages have made them a popular choice in modern electronic designs that demand both reliability and efficiency.
These PCBs have a metal (usually aluminum) base instead of the standard fiberglass. This enhances heat dissipation.
Advantages:
· Great thermal management
· Strong and durable
· Cost-effective for power applications
Applications:
· LED lighting
· Power converters
· Motor controllers
HDI (High-Density Interconnect) PCBs
HDI (High-Density Interconnect) PCBs are advanced circuit boards that offer a higher wiring density per unit area compared to traditional PCBs. They feature finer lines and spaces, smaller vias (including microvias, blind vias, and buried vias), and higher connection pad density, allowing for more compact and complex designs. HDI technology is essential for miniaturized electronics, enabling the integration of more components in a smaller footprint while improving electrical performance and signal integrity. These boards are widely used in cutting-edge devices such as smartphones, tablets, wearables, and aerospace or medical equipment, where space-saving and high-speed signal transmission are critical.
HDI PCBs have a higher wiring density than standard boards. They use microvias, blind and buried vias, and fine lines.
Advantages:
· Space-saving design
· Improved electrical performance
· Better signal integrity
Applications:
· Smartphones
· Tablets
· Medical and aerospace equipment
The type of PCB you choose depends on your application’s complexity, size constraints, environmental factors, and cost considerations. Whether it's a simple single-sided board or a sophisticated HDI multilayer PCB, understanding each type ensures the right foundation for building reliable electronic products.
Choose PCBLONGYU
At PCBLONGYU, we specialize in providing all types of PCBs to meet the unique needs of your project—whether it’s a simple single-sided board or a complex HDI multilayer design. With our expertise, advanced manufacturing capabilities, and commitment to quality, we ensure you get reliable, high-performance PCBs tailored to your exact specifications. No matter the industry or application, we’re here to support your innovation from prototype to production. Choose PCBLONGYU as your trusted PCB partner and experience excellence at every layer.
Types of PCBs, Single-sided PCB, Double-sided PCB, Multilayer PCB, Rigid PCB, Flexible PCB, Rigid-Flex PCB, High-Frequency PCB, Aluminum-backed PCB, HDI PCB, Printed Circuit Boards, PCB manufacturing, PCB design, PCB applications, PCB materials