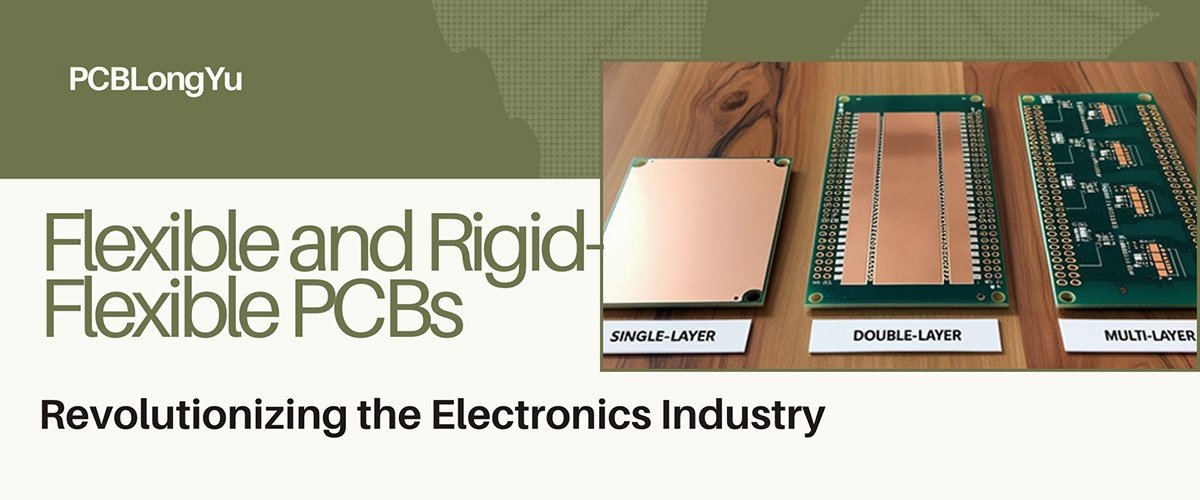
The world of electronics is evolving rapidly, and at the heart of this transformation are flexible and rigid-flexible printed circuit boards (PCBs). These innovative PCB designs have paved the way for modern electronics, offering solutions that go beyond traditional, rigid PCBs. Whether you're in the consumer electronics, automotive, aerospace, or medical industries, understanding how flexible PCBs (FPCs) and rigid-flexible PCBs are shaping the future is crucial.
What Are Flexible PCBs?
Flexible PCBs, often referred to as flex circuits, are electronic circuits that can be bent or folded without losing their functionality. Unlike rigid PCBs, which are usually made of inflexible substrates, flexible PCBs use flexible materials such as polyimide or polyester film. These materials provide outstanding flexibility, which is perfect for applications requiring space-saving designs and lightweight circuits.
Key Advantages of Flexible PCBs:
1. Space Efficiency: Flexible PCBs can be bent, folded, or twisted to fit into complex, confined spaces, making them ideal for compact, lightweight devices.
2. Durability and Flexibility: Flexible PCBs withstand bending and twisting, leading to fewer chances of breakage, particularly in products that experience physical stress.
3. Reduced Wiring: The flexibility eliminates the need for multiple wires, simplifying the design and reducing the number of connections needed.
4. Lightweight Design: These PCBs are lighter than rigid PCBs, which is beneficial for portable and wearable devices.
Common Applications of Flexible PCBs include:
1. Wearable devices (smartwatches, fitness trackers)
2. Medical devices (implants, hearing aids)
3. Consumer electronics (smartphones, tablets)
4. Automotive (instrument clusters, electric vehicles)
Related Link: Explore Our Range of Flexible PCBs for Advanced Applications
What Are Rigid-Flexible PCBs?
Rigid-flexible PCBs combine the advantages of both rigid and flexible PCBs, creating a hybrid solution for industries that require high-density designs in flexible forms. As the name suggests, a rigid-flexible PCB integrates both rigid and flexible elements within the same circuit board. The rigid sections provide mechanical support, while the flexible sections allow for adaptability and compact design.
These boards are designed to fit the most intricate product shapes and serve the growing need for miniaturized electronics with high reliability.
Key Advantages of Rigid-Flexible PCBs:
1. Complex Design Flexibility: Rigid-flexible PCBs allow for high-density circuit designs that fit in small spaces, supporting multiple layers in confined forms.
2. Enhanced Durability: The rigid areas provide structural stability, while the flexible parts allow movement, making them ideal for demanding applications that require flexibility without compromising on durability.
3. Reduced Assembly Time and Costs: By combining multiple functions into a single PCB, rigid-flexible PCBs reduce the need for complex interconnections, which can lower assembly time and costs.
4. Weight and Size Reduction: These PCBs contribute to the overall reduction in the weight and size of devices, an essential factor in applications like aerospace and medical devices.
Common Applications of Rigid-Flexible PCBs include:
1. Aerospace (communication systems, satellites)
2. Medical devices (surgical instruments, diagnostic equipment)
3. Automotive (infotainment systems, EVs)
4. Consumer electronics (smartphones, laptops)
Related Link: Discover Our PCB Solutions for the Future of Electronics
Why Choose Flexible and Rigid-Flexible PCBs?
The choice between flexible PCBs and rigid-flexible PCBs largely depends on the application and the unique requirements of the project. However, both offer advantages that set them apart from traditional rigid PCBs:
* Compactness: Both types allow for more compact designs, which are crucial for modern, portable devices.
* High Reliability: With fewer interconnections and components, flexible and rigid-flexible PCBs tend to be more reliable, especially in environments where vibration, motion, and space constraints exist.
* Cost-Effective: While they might be more expensive upfront, flexible and rigid-flexible PCBs can reduce overall product assembly costs and improve the longevity of devices by minimizing breakage risks.
Applications Driving the Future
Flexible and rigid-flexible PCBs are becoming an integral part of the electronics industry, as industries evolve towards smaller, smarter, and more adaptable devices. As demand grows for devices with compact designs, wearable technology, and automation systems, these types of PCBs are expected to dominate the market. The ability to provide more compact, durable, and flexible solutions will continue to drive innovation in sectors such as:
* Medical: Devices that need to be lightweight and flexible for wearables or implants.
* Aerospace: Communication systems where durability and adaptability are crucial.
* Consumer Electronics: Smartphones, tablets, and wearables that require thin, flexible, yet reliable electronics.
Related Link: Contact Us for Custom PCB Solutions
The evolution of flexible and rigid-flexible PCBs is a testament to the technological advancement of the electronics industry. These boards are enabling manufacturers to produce more compact, durable, and functional devices. As industries continue to demand more adaptable and space-efficient designs, flexible and rigid-flexible PCBs will play a pivotal role in shaping the next generation of electronics.
Ready to innovate with flexible and rigid-flexible PCBs? Explore our custom PCB solutions that meet the needs of today's rapidly advancing technologies. Get in touch with us to discuss how our PCBs can elevate your next project.